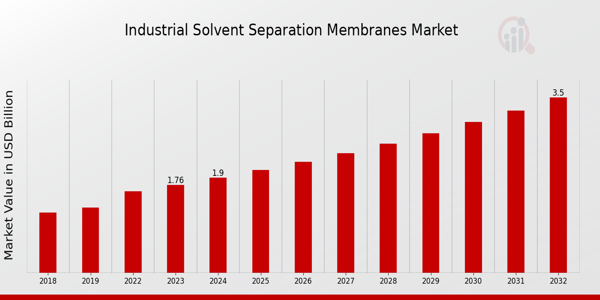
Introduction
In the ever-evolving landscape of industrial processes, efficiency and sustainability have become paramount. One of the most groundbreaking advancements in recent years is the development and adoption of industrial solvent separation membranes. These innovative membranes are transforming how industries handle solvent recovery, purification, and waste management, offering a greener, more cost-effective alternative to traditional methods.
What Are Industrial Solvent Separation Membranes?
Industrial solvent separation membranes Market are specialized filters designed to separate solvents from mixtures based on their molecular size, polarity, or other chemical properties. These membranes are typically made from advanced materials such as polymers, ceramics, or composites, which are engineered to withstand harsh chemical environments and high temperatures.
The primary function of these membranes is to selectively allow certain molecules to pass through while blocking others, enabling the separation of solvents from complex mixtures. This technology is particularly valuable in industries where solvent recovery and purification are critical, such as pharmaceuticals, petrochemicals, food and beverage, and electronics manufacturing.
Why Are They Gaining Traction?
Environmental Sustainability: Traditional solvent separation methods, such as distillation, often require significant energy input and can generate harmful emissions. In contrast, membrane-based separation operates at lower temperatures and pressures, reducing energy consumption and minimizing environmental impact. This aligns with global efforts to reduce carbon footprints and adhere to stricter environmental regulations.
Cost Efficiency: While the initial investment in membrane technology can be higher, the long-term savings are substantial. Membranes reduce the need for energy-intensive processes, lower solvent waste, and extend the lifespan of solvents by enabling their reuse. This translates to significant cost savings for industries over time.
Enhanced Purity: Solvent separation membranes offer unparalleled precision in separating solvents from complex mixtures. This results in higher purity levels, which are crucial in industries like pharmaceuticals, where even trace impurities can compromise product quality.
Versatility: These membranes can be tailored to specific applications, making them adaptable to a wide range of industries. Whether it’s recovering ethanol in biofuel production or purifying solvents in chemical manufacturing, the technology can be customized to meet unique requirements.
Key Applications
Pharmaceuticals: In drug manufacturing, solvents are often used in large quantities for synthesis and purification. Membrane technology allows for the efficient recovery and reuse of these solvents, reducing costs and minimizing waste.
Petrochemicals: The petrochemical industry relies heavily on solvents for various processes, including extraction and refining. Solvent separation membranes enable the recovery of valuable solvents from complex hydrocarbon mixtures, improving efficiency and reducing environmental impact.
Food and Beverage: In the production of flavors, fragrances, and essential oils, solvents are used to extract desired compounds. Membranes help in recovering these solvents, ensuring product purity and reducing waste.
Electronics: The electronics industry uses solvents for cleaning and degreasing components. Membrane technology aids in the recovery and recycling of these solvents, contributing to more sustainable manufacturing practices.
Challenges and Future Outlook
Despite their numerous advantages, industrial solvent separation membranes are not without challenges. Membrane fouling, where the membrane becomes clogged with particles or contaminants, can reduce efficiency and require frequent maintenance. Additionally, the development of membranes that can withstand extreme chemical and thermal conditions remains an ongoing area of research.
However, advancements in material science and membrane design are rapidly addressing these issues. Researchers are exploring novel materials, such as graphene and metal-organic frameworks (MOFs), which offer superior chemical resistance and selectivity. Furthermore, the integration of artificial intelligence and machine learning into membrane systems is enabling real-time monitoring and optimization, further enhancing their performance.
Conclusion
Industrial solvent separation membranes are poised to revolutionize how industries manage solvents, offering a sustainable, cost-effective, and efficient alternative to traditional methods. As technology continues to advance, these membranes will play an increasingly vital role in driving industrial innovation and environmental stewardship.
For industries looking to stay ahead of the curve, investing in solvent separation membrane technology is not just a smart business decision—it’s a commitment to a more sustainable future. As we move towards a greener economy, these membranes will undoubtedly be at the forefront of industrial transformation.
Parking lot security is often overlooked but vital. Security guards patrol parking facilities to prevent vehicle theft and vandalism. They also assist guests in navigating the securitycompaniesnearme.com area safely and respond promptly to any issues, maintaining security even outside the main hotel building.